Manufacturers Index - Cincinnati Planer Co.
Cincinnati Planer Co.
Cincinnati, OH, U.S.A.
Manufacturer Class:
Metal Working Machinery
Last Modified: Jul 10 2022 12:40PM by Jeff_Joslin
If you have information to add to this entry, please
contact the Site Historian.
|
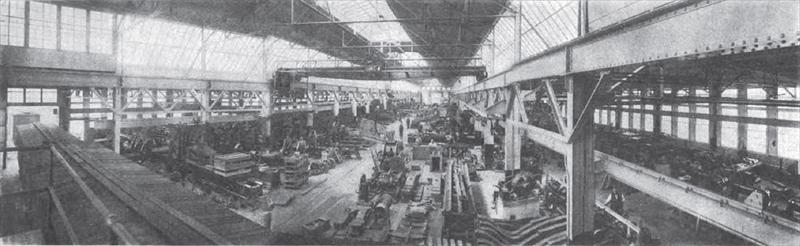 |
Cincinnati Planer Co.—Shop Floor View |
In 1898 Bertram B. Quillen, Reuben A. Holden and William H. Burtner formed a partnership to design and manufacture a metal planer. The Cincinnati Planer Co. was formally chartered in March of 1899. A month later they completed and shipped their first planer from their factory on Buck Street in Cincinnati; another 65 planers were shipped that year.
In 1900 their planer won a Gold Medal at the Paris Exposition, and with that publicity they were able to establish a dealer network in Europe. In 1904 Burtner, who was in failing health, was bought out by C. H. M. Atkins who became president of the company. In 1910 the company relocated to a new factory in the Cincinnati suburb of Oakley, where they would remain for forty years. In 1911 they shipped their first boring mill. Production of planers, boring mills and turning mills all greatly increased during World War I.
Meanwhile, the owners of the company were acquiring other local machinery manufacturers including engine lathe maker Champion Tool Works, turret lathe maker Acme Machine Tool Co., and woodworking machinery maker Greaves-Klusman Tool Co.
In 1920 Atkins became chairman of the board and B. B. Quillen, who was the largest shareholder, took over as president of the Cincinnati Planer Co., a role he would occupy until his death in 1945. At that time the vice president and factory manager was Frank Langen, who had been with the company and since 1898. In 1946 Quillen's heirs sold out to local investors Sidney G. Rose, Philip L. Moskowitz and Ben Moskowitz. At that time Langen became president and Rose became chairman of the board. Then in July of 1948, the Rose-Moskowitz syndicate sold out to Giddings & Lewis Machine Tool Co. of Fond du Lac, Wisconsin. One year later Cincinnati Planer sales and engineering departments were moved to Fond du Lac, and a year after that the rest of the company was moved.
Information Sources
- 1902-06-12 The Iron Age.
The Whalen Planer Tool.—The accompanying cut represents a new combination planer tool which is being put on the market by the Cincinnati Planer Company of Cincinnati. The tools is formed with an apron and tool block and is provided with a turret movement that works in the end of the shank. It will cut in any position desired, across a surface, down the sides, and do right or left undercutting. In order to set the turret, the nut in the rear is loosened and the thumb nut at the side screwed down. The latter operation withdraws the locking pin, leaving the turret free to be set in any position. The main object of the tool is to do away with the lifting or dragging of large and heavy tools on the return stroke when planing side work or undercutting. It is particularly useful for planing slots in the side of a piece where a side head cannot be used to good advantage.
- 1902-08-09 Timber & Wood-Working Machinery.Whalen Planer Tool.—A new combination planer tool is being put on the United States market. It is formed with an apron and tool block..." The rest of the text is virtually identical to that of the early notice in The Iron Age, but the "being put on the United States market" is notable because it implies that the tool was developed elsewhere.
- 1905-01-19 The Iron Age.
Business Changes—The Cincinnati Planer Company of Cincinnati, Ohio has increased its capital stock to $200,000, and elected the following officers: C. H. Atkins, president; B. B. Quillen, secretary and treasurer; Geo. Langen, general superintendent; these officers together with E. N. Atkins and C. M. Quillen make up the directory. W. H. Burtner, former president of the company, retires on account of poor health. Mr. Atkins, the new president, is also president of the Warner Elevator Company and the Norwood National Bank, and is connected with several other leading concerns of Cincinnati.
- 1908-10-29 The Iron Age.
Planers.—Cincinnati Planer Company, Cincinnati, Ohio. Catalogue No. 10. Size, 6 x 9 in.; pages, 56. Contains general descriptions and illustrations of Cincinnati planers... the Whalen platnet planer tool and other planer tools...
- 1910 Railway Master Mechanic by the Railway List Co., pages 456-459.
The Cincinnati Planer Co. is now occupying a new plant at Oakley, OH., a suburb six miles from Cincinnati. It has a nine-acre tract on which it has erected a one-story brick and steel structure 150 ft. wide by 400 ft. long and a separate office building of two stories. This building immediately adjoins the front end of the shop, separated by a brick wall with two entrances, which are protected by automatic fireproof doors. The shop is equipped with two electric cranes, one of 15-ton and another of 20-ton capacity. These large cranes are used in handling the heavy planer beds and tables and in serving the big tools located in various departments along the main aisle. In the west bay is a 5-ton Pawling & Harnischfeger electric crane and in the east bay a 4-ton Shepherd crane, both controlled from the floor. These crapes are used in handling the rails and other smaller parts of the machines. In the front end of the shop is a depressed track, of sufficient length to admit two 40-ft. cars and so located that both cars can be loaded or unloaded at the same time by use of the large cranes in the main aisle and the 5-ton crane in the west bay, this railroad track being used mainly for shipping. On the west side of the building there is another spur used for receiving castings and raw material in carload lots. This spur runs through the casting yard located in the rear of the building. Cars are unloaded with an electric crane, which travels over the cars and the full width of the building.
Each department is driven by an individual motor, the line shafts being put up in short sections, making each department independent of the others. All the larger tools are driven by motors mounted direct on the machines. Hyatt roller bearings are used on all line shafting throughout, reducing the friction to a minimum. The motors are mounted on concrete piers about 3 ft. high, where all cars and adjustments can be made readily from the same floor. All the heavy tools are mounted on solid concrete foundations, the lighter machines setting direct on the floor. In the planer department, located in the northwest end of the building, ;ill the heavier planers are mounted on improved leveling wedges, which arc embodied in concrete, making these tools solid on their foundations. These wedges also enable accurate adjustments when releveling after inspection every few months, therefore insuring the work coming from these machines, such as beds, tables, housings and rails, being planed perfectly, requiring little or no scraping. The greatest care is exercised in the planing operations, especially on such work as is likely to spring when released from the clamps. This is especially noticeable in the planing of tables. To secure the best results, the casting is first completely roughed, then drilled and allowed to lay for a few Jays, giving it time to resume its natural form, after which it is returned to the planer for finishing. On small work like gibs, the same practice prevails.
The lathe department, located in the northeast end of the building, receives its raw material and castings by trucks over an industrial track from the casting yard. All the various boring lathes and mills are arranged at this entrance. The castings, being first bored and rough turned, pass down to the different lathes for finishing, then to the grinders, and into the milling department, but never crisscross anywhere throughout the shop. The heavier machines in this department are equipped with single I-beam cranes. Shafts are made of high carbon steel and are first turned, key-wayed and then ground. All spur, bevel and mitre gears are cut on automatic machines of the latest type. All driving gears are cut by a system of special cutters for each gear, thereby obtaining perfect rolling spur gears. All bevel and mitre gears are matched and tested on a special testing machine. The table rack, which is cut with special cutters or tools on the planer, is also tested and matched in this department, using a large spur gear with corresponding pitch. All boring and drilling is clone by jigs in the drill press department, which is centrally located in the shops. A novel feature of this department is the system of driving all tools from a single line shaft, no countershafts being used. Beds and housings are also drilled by jigs, the boring bars being driven by knuckle joints, doing away with all side thrust, giving a perfect circumference to all work done in this manner.
The distributing and stock room is located in the center of the shop, where all jigs, tools, screws, drawings and supplies are to be had, thus making it accessible from all departments. The main erecting floor occupies a large portion of the main aisle, where it can also be served by the large cranes. The large pit for erecting the big boring mill is also in this department. There are three test shafts in this department, each driven by individual motor of reigning capacity. The final tests of every planer are made under these shafts, where the feeds are tried and the machine finished by taking a cut off the table on its own bed and the tee slots finished to standard plugs. All finished work is brought here to be matched and fitted. The housings, rails, etc., are all scraped to surface plates, using straight edges and indicators in squaring them with one another.
A word about the principal features of the finished machines: Take, for example, a 30-in. standard planer. It will be noticed that the bed is bored out -to a jig,-it is especially strengthened where the gearing and housings are mounted, and is braced at short intervals with heavy box girths. The ways are hand scraped and are fitted with a series of automatic oilers, which keep the tees thoroughly lubricated. The shaft bearings or boxes are ground and fitted solidly into the bored holes in the bed, and have oil grooves that furnish a sufficient supply of oil. The driving shafts are made from high carbon crucible steel, and after being turned and keywayed, they are ground to insure the greatest possible accuracy. The pulley shaft, which is the only high speed shaft in a planer, is made ring oiling. All gears are cut from solid stock, semi-steel being used in the large gears and steel forgings for the pinion. They are placed on the inside of the bed, obviating all danger to the workman and protecting the gears from dirt and chips. The table is of considerable depth, and is braced and thoroughly ribbed underneath, insuring unusual stiffness. It is fitted with a dirt-proof feature, which prevents chips from falling into the tees. Holes are drilled and reamed from the solid and T-slots planed its entire length. The housings are carried down to the bottom of the bed, and are fastened to it by heavy bolts and dowel pins. They are braced by a box shaped arch at the top, giving great rigidity and resistance to jar from heavy cuts when tools are at the highest point. The face of the housings are scraped to surface plates and great care is taken in fastening them to the bed, so that they are parallel with each other and are square with the bed. The housings are also held in place by tongue and groove, preventing spring under heavy work.
The cross rails are accurately scraped to straight edges and surface plates. They have a generous bearing on the housings, which are scraped on the front and back. The rail is made of sufficient length to allow either head to have full traverse across the table. The heads are carefully scraped to the rail and are graduated for swiveling up to 90 degrees. They are of a new shape, the end of tool block and slide being made round to avoid projecting corners on angular work. The heads have adjustable taper gibs on the down slide and the front and rear of saddle. The slides are hung on ball bearings, allowing them to work easy, and both heads can be raised at the same time with very little effort. They are right and left and are provided with automatic feeds in all directions. The tool block swings on a tool steel taper pin and carries four heavy steel bolts for clamping the tools. A power elevating device is furnished on all machines with double head rails, being operated by friction rings, and it is noiseless and is subject to very little wear. Being in the center of the arch, it exerts equal tension on the elevating shaft. A bearing next to the large raising gear does away with any side thrust that may occur. The gears are so arranged that a slow speed is used for raising and a fast for lowering. The device is engaged by a long handle at the side and when idle is locked by a binding screw. The pulley and shaft are the only revolving parts when not in use.
- See 1917 ad from Cincinnati Planer Co.
- July 1919 Machinery.
Acme Machine Tool Co. and Greaves-Klusman Tool Co., Cincinnati, Ohio, will be located in the new plant of the Champion Tool Works Co., at Spring Grove Ave., and Winton Place, Cincinnati, which has been purchased by C. H. M. Atkins, B. B. Quillen, and their associates, from H. W. Kreuzburg and A. H. Rosenberg. The buildings are of brick and steel construction, sawtooth roof, located on the main line of the Baltimore & Ohio Railroad, and cover approximately 100,000 square feet of floor space on a trace of land six acres in extent. The purchases of the property control the Acme Machine Tool Co., the Cincinnati Planer Co., and the Greaves-Klusman Tool Co., and when the Acme and the Greaves-Klusman companies are located in the newly acquired buildings it is planned to add other buildings to the plant, by which arrangement it is expected to make this concern one of the largest manufacturers of machine tools in Cincinnati, employing approximately 1000 men.
- 1946 issue of The Iron Age (volume 157, page 1946-152). "Cincinnati Planer Co. was bought last week by a group headed by Sidney G. Rose , Philip L. and Ben Moskowitz in a transaction involving approximately $3,500,000. Mr. Langen, who had been vice-president, and factory manager of the company since its inception, was named president, and Mr. Rose..."
- 1946-03-14 issue of American Machinist (volume 90 #6, page 148i).
Cincinnati Planer Co. Sold; Langen President
CINCINNATI — The Cincinnati Planer Co. was acquired for about $3,500,000 by a local group headed by Sidney G. Rose, Philip L. Moskowitz and Ben Moskowitz. The company will continue under the management of George Langen, former vice president, who will become president, while Mr. Rose becomes chairman of the board. Other officers will include: Philip Moskowitz, vice president; Verner Schoolfield, vice president and treasurer; John H. Daum, vice president in charge of sales, and Ray J. Steiner, secretary. Except for Moskowitz and Rose, all of these officers had been connected with the former company.
Mr. Langen had been factory manager of the company since its inception in 1898, when it was founded by Bert B. Quillen, president and principal stockholder, who died a year ago. The remainder of the company’s personnel is also being retained.
Mr. Rose is also president and general manager of Cleveland Wrecking Co., Rose Brothers Co., Associated Building Wreckers & Materials Co., and managing head of the Empire Case Good Co., Frederick Iron & Steel Co,. and Hoosier Cabinet Co.
- 1948 issue of Machinery (volume 54 issues 7-12, page 176).
Fiftieth Anniversary of Cincinnati Planer Co.
FIFTY years ago, Bertram B. Quillen, William H. Burtner, and R. A. Holden, all of Cincinnati, formed a partnership to engage in the manufacture of metal-working planers. This partnership continued until early in March, 1899, when a charter of incorporation was granted by the State of Ohio, at which time the corporation was named the Cincinnati Planer Co. The original plant was located on Buck St. in the West End of Cincinnati. The first planer was completed on April 21, 1899, and sixty-five additional planers were built and shipping during the same year.
In a short time, the company reached out for the export trade. The first planer shipped to Europe was exhibited at the Paris Exposition in 1900, at which time the company received a Gold Medal Award from the Republic of France. Soon afterward the company entered into many exclusive dealer arrangements for the sale of its products. Some of these dealers still represent the company, although they have been...
In 1910, buildings and part of the machinery of the old plant located on Buck St. were sold and the new building in Oakley was occupied. This is still the location of the company.
In 1911, the company expanded its products and added a vertical boring mill. During the first World War the Cincinnati Planer Co. contributed greatly to the machine tool requirements of the nation by furnishing planers and vertical boring and turning mills. In 1917, the buildings were expanded, doubling the floor space of the Oakley plant. During the following years the company acquired the buildings and machinery to other companies, including the Advance Tool Co., Greaves-Klusman Machine Tool Co., Champion Tool Works, and the Cincinnati Automatic Screw Machine Co. Some of these properties were later sold.
In 1920, Mr. Atkins became chairman of the board, and B. B. Quillen became president. Five years later, the company began manufacturing ...
- March 1950 Western Machinery and Steel World (volume 41, page 117), in the News of the Industry column.
All operations of the Cincinnati Planer Company now functioning at Cincinnati, Ohio, will be moved to Fond du Lac, Wisconsin, and absorbed by the parent organization, the Giddings & Lewis Machine Tool Company. The move to combine operations at Fond du Lac was decided for reasons of reducing general operating costs and to provide more extensive engineering and research facilities. It is anticipated that the move will be completed by July 1, 1950.
R. J. Kraut, president and general manager, emphasized that the Cincinnati Planer Company was in no being liquidated and plans for moving the complete operation to Fond du Lac have been so set up as not to jeopardize sales and delivery of the planer company products. The complete machine tool line regularly manufactured in Cincinnati will now be built in the new and modern building which were especially designed for machine tool manufacturing. The Cincinnati Planer Company was purchased by the Giddings & Lewis Machine Tool Company in July 1948. In July of 1949 the sales and engineering departments of the two companies were consolidated and transferred to Fond du Lac.
- A 1959 lawsuitincludes the testimony of one Jacob Walter Knippling, who for 18 years, 1932 to 1950, was a purchasing agent for Cincinnati Planer Company. "In 1950 we sold out to the Moskowitz Road Syndicate, and they in turn sold us to the Giddings & Lewis Company of Fond du Lac, Wisconsin." Later, when asked when he left the employ of the Cincinnati Planer Company, he replied, "June 15, 1950".
- American Planer, Shaper and Slotter Builders: 1830-1910 by Kenneth L. Cope, 2002 page 37
|